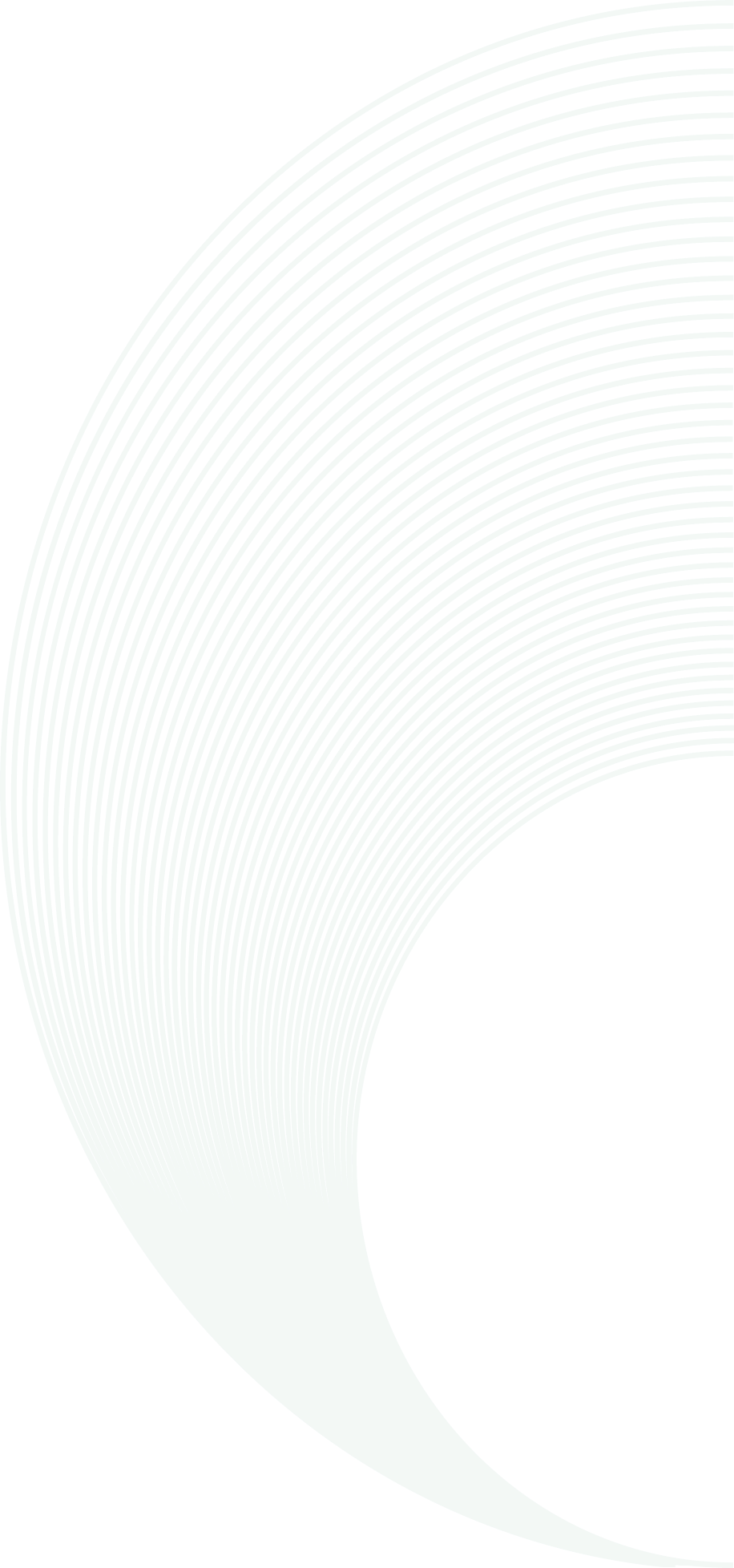
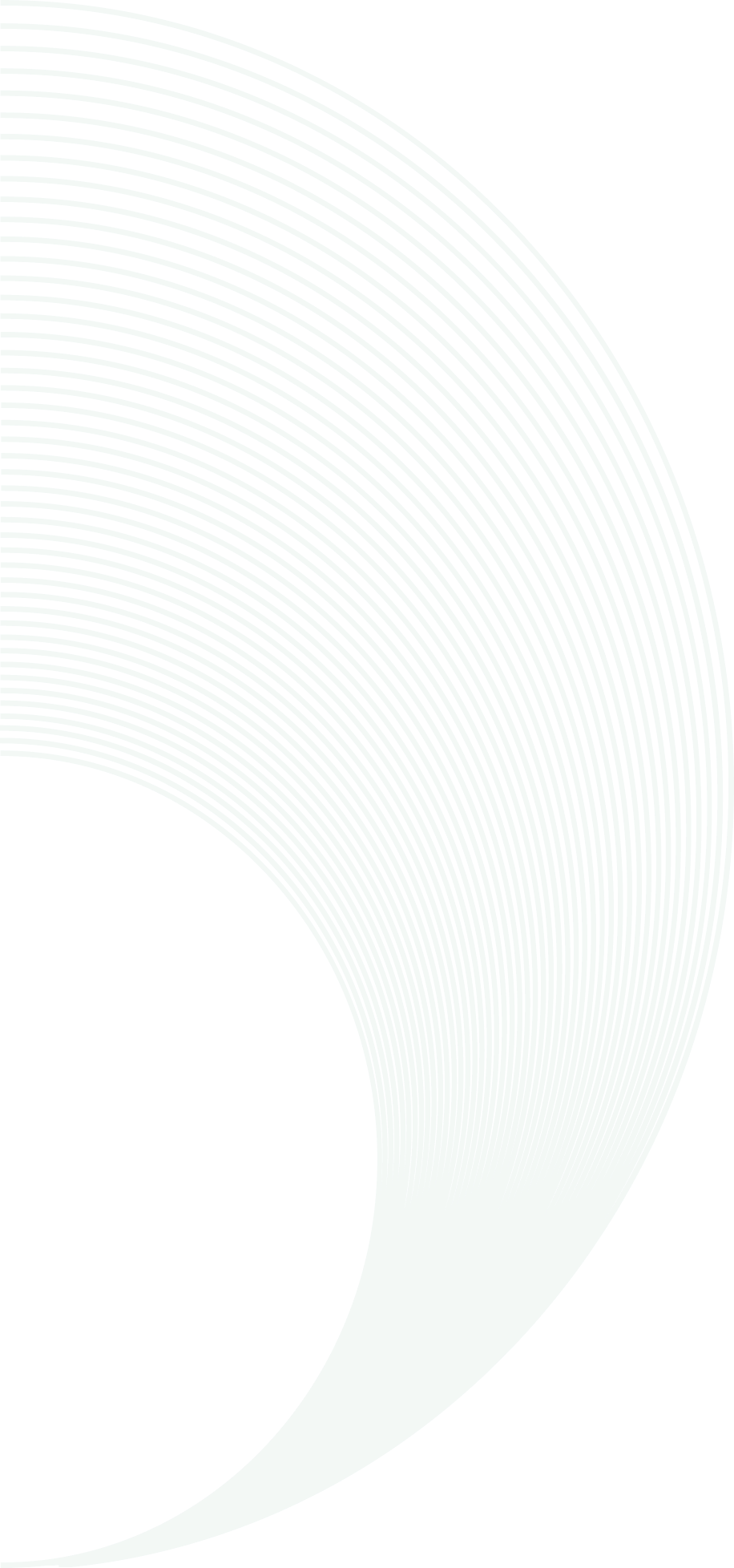
Choosing the Right Laser Cutting Machine for Your Business
Discover how to choose the right laser cutting machine for your business. Compare features, materials, and capabilities to make an informed decision.
Laser-cutting technology is the core of precision manufacturing and is applied in various industries, including automotive, aerospace, electronics, and fashion. It has the ability to produce intricate designs with high accuracy, which makes it indispensable for many applications, such as metal and plastic cutting, fabric and woodwork. The right laser-cutting machine must be selected for businesses because the machine should meet specific production needs, material requirements, and budget constraints.
Laser Cutting Technology
Laser cutting technology focuses a high-energy laser beam on materials to cut or engrave them. The intense heat from the laser vaporizes or melts the material along the cutting path, giving smooth and precise edges. There are various laser types, each suitable for different materials and cutting applications.
- CO2 Lasers: Suitable for cutting non-metallic materials such as wood, acrylic, and textiles and can be economical in terms of non-metal application.
- Fibre Lasers: These lasers produce the type of high power density required to cut thin metals. The speed is relatively faster with high efficiency.
- Solid-State Lasers: Because of their flexibility in providing precision with various applications in cutting, these lasers can be used with an extensive range of materials from metallic to non-metallic.
Factors to Consider Before Choosing a Laser Cutting Machine
When determining laser cutting machines, there are key performance-related and cost considerations:
- Output: The direct influence of power will be used in the output cutting, maximum thickness materials that one can cut as well as the general output in terms of cut quality. Power machines require thicker cuts at an increased rate and increased costs for working.
- Cutting speed: An organization that needs to work on high production volumes with the use of the business will benefit significantly through the ability to increase productivity through production time minimization. When using this attribute, identify the minimum requirements regarding cutting speed because it must cut for your given business need on a productivity basis.
- Material Compatibility: The lasers are optimized for material compatibility. Test if the machine can cut most of the materials your company regularly uses, whether metals, plastics, or fabrics.
- Cutting Precision: If a design has fine detail or needs to be within a very close tolerance, cutting should be precise. A high-precision laser is needed to produce a clean cut with less scrap and possibly no finishing work.
- Size and Workspace: Determine your workplace's physical space by its dimensions and the scale of materials you intend to work with. A greater-sized machine will occupy additional physical space but can host a bigger material or produce bulk cuts.
- Maintenance Costs/ Operating Expenses: Maintenance charges as well as replacement and fuel consumption are also considerable expense elements. Choosing to install a model that boasts minimum operational costs will weigh hugely in the long run on payback.
Comparison of Different Types of Laser Cutting Machines
- CO2 Laser Cutting Machines: CO2 lasers are very versatile and cheaper to begin with. While they can be good for cutting non-metallic materials, their speed on metals is generally slow. CO2 lasers are best suited for small business setups or those that use acrylics or textiles.
- Fiber Laser Cutting Machines- These are the most powerful high-speed machines with the highest power density. These have special suitability for cutting in metals. The quality of beams is better with the resulting cuts and can process quicker in comparison. Therefore, the ideal applications include more metal-based industries.
- Solid-State Laser Cutting Machines: They are flexible machines with high-precision cuts across various materials. They balance between CO2 and fibre lasers and are ideal for those who need both metal and non-metal capabilities.
Cost Effectiveness of Laser Cutting Machines
Understanding the cost dynamics is essential to making a well-informed investment:
- Initial Capital Input: Here you pay the extra charges over the core value for your laser machine such as adding more software that could come along, and more for setting and mounting components.
- Cost to run a Laser machine; This includes all that runs it that one requires when making cutting using this product like buying Laser Nozzles gas for making all operations while ensuring services about machines that operate on such things, but such machines, like some people always make in choosing equipment not a piece of jewellery at its start that operates optimally since most run due to minimal use to last in any machine as any given above.
- Labour Costs: Automation through laser cutting will reduce the demands of manpower and increase productivity. More than often, the use of machines with automated capabilities is likely to require smaller labour inputs thus lowering the overall labour cost.
- ROI: Determining the ROI would be measured through production increase potential quality improvements and reduced labour. On average, higher efficiencies do mean greater profitability. And that is what, one is likely to need, for paying off the expenses associated with the machine to establish it.
Conclusion
The choice of the proper laser-cutting machine thus falls between technical capabilities and business needs, such as the power output, the compatible materials, and all those cost factors. Detailed research, consultation with professionals within the industry, and comparative examination of machines according to production requirements can help decide appropriately. Investing in a laser cutting machine that is capable in terms of efficiency produces better quality products, bringing any business closer to sustaining competitive market success over the long run.