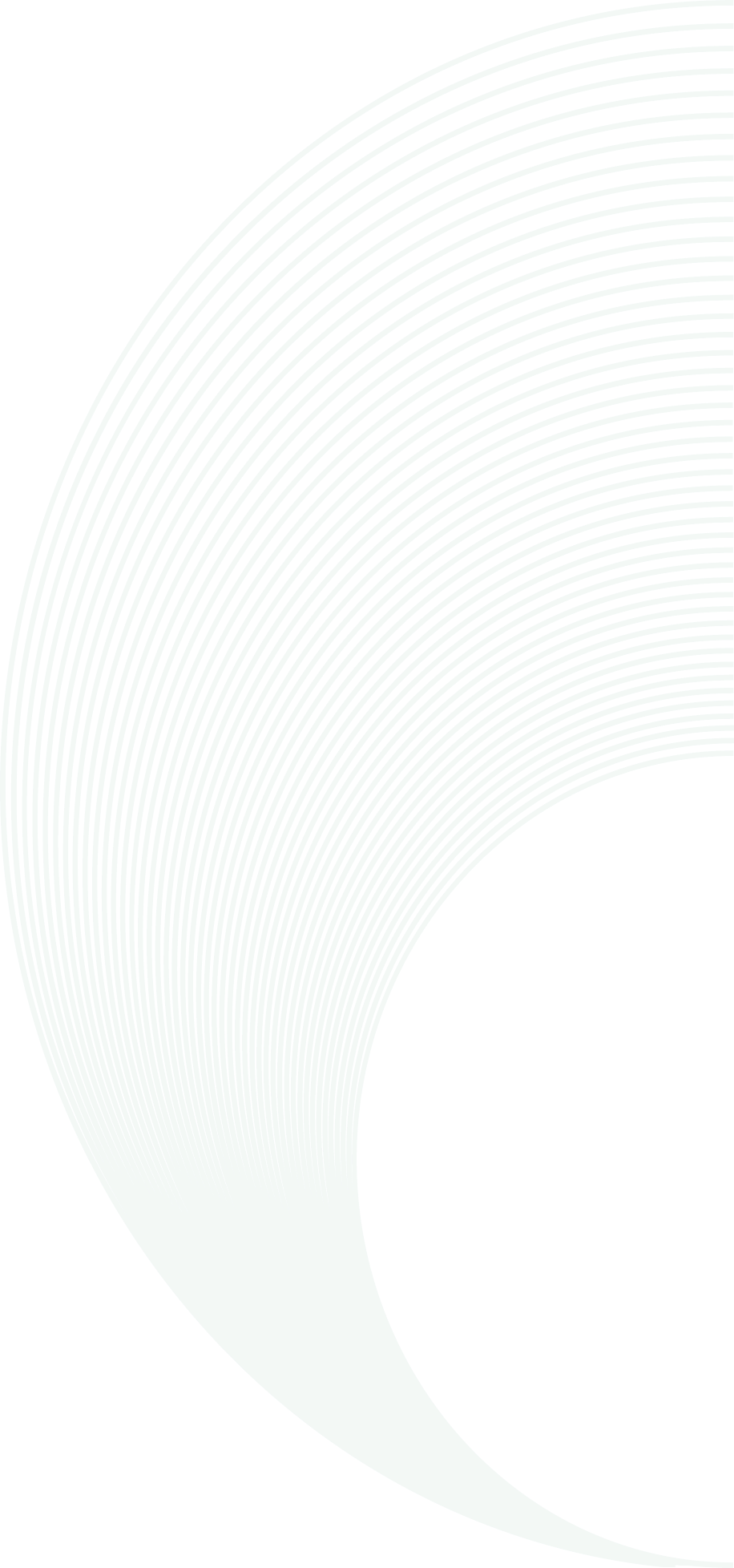
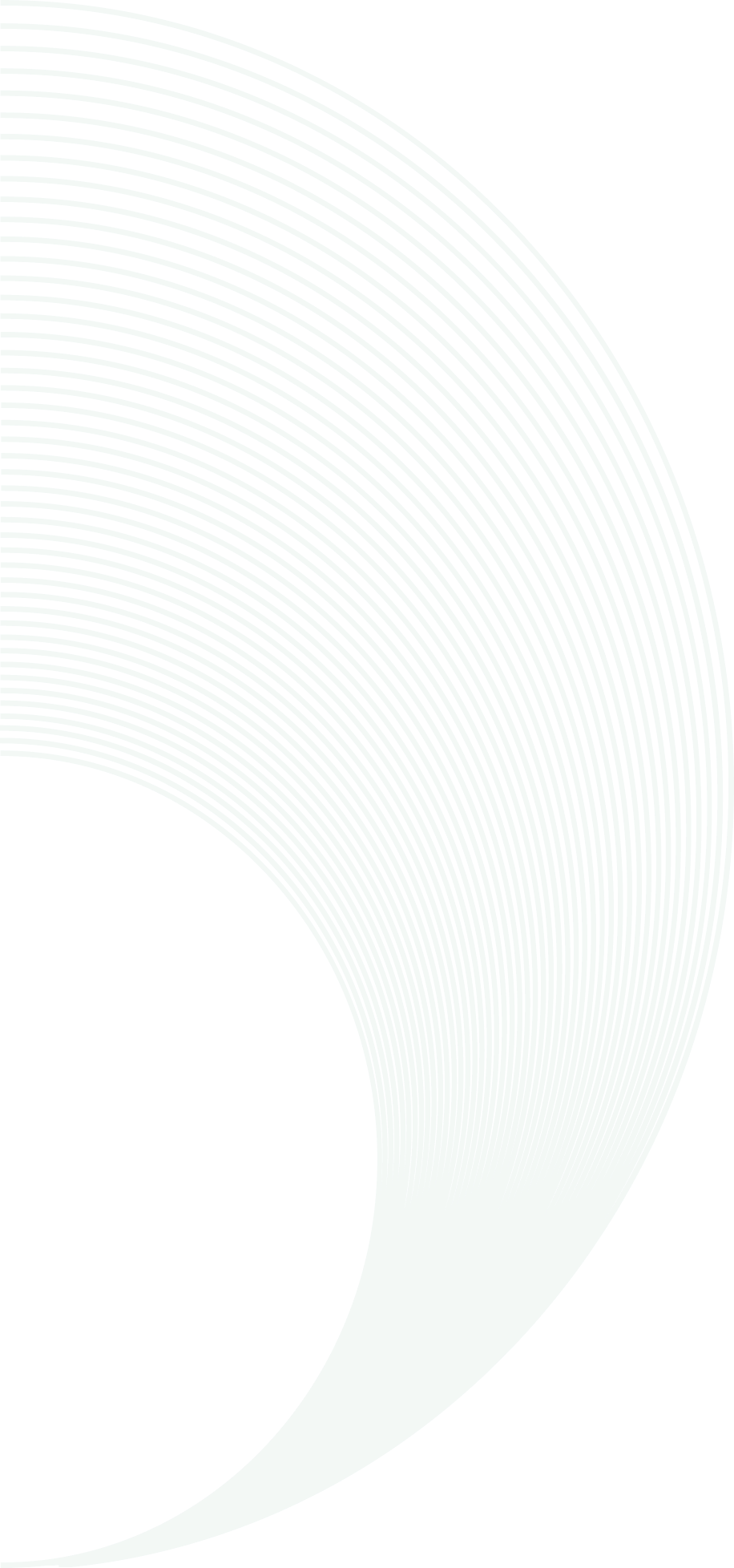
The Future of Conveyor Systems: Automation and Innovation
Explore the future of conveyor systems with advancements in automation and innovative technologies, driving efficiency and productivity in industries.
Conveyor systems have been in place for ages as part of the manufacturing, warehousing, and logistics industries. The proper movement of goods is crucial for these industries, and it's a matter of huge concern. Material flow and labour costs are reduced when the operations are streamlined using conveyor systems. As time goes by, demands grow to be faster, more flexible, and more efficient, thus increasing the need for innovation in conveyor technology. From the latest autonomous mobile robots to advanced sensor systems, conveyor systems look to change the face of manufacturing and logistics going forward.
The smart factory, which integrates machines, devices, and systems connected to make production processes easier and boost operational efficiency, is the core concept in Industry 4.0. From the key areas of material handling, it is here that conveyors are part of an altered direction related to the concept of the smart factory.
The core of the change is in automation technologies, including artificial intelligence, machine learning, and robotics. AI algorithms allow the conveyor system to adjust in response to changes in demand and optimize workflows, while machine learning allows predictive maintenance by looking at historical data to predict equipment failures. These innovations allow businesses to streamline their operations, minimize downtime, and maximize productivity, thus making conveyor systems highly valuable assets in Industry 4.0 environments.
Autonomous Mobile Robots in Conveyor Systems
These AMRs move materials through facilities on their own by adapting in real-time to changes in their environment through sensors, cameras, and onboard navigation systems. Unlike traditional conveyors, which follow fixed paths, AMRs can change their route dynamically according to traffic, obstacles, and job priorities. This type of flexibility enables them to support complex logistics workflows that reduce the need for human intervention.
Advantages of employing AMRs in conveyor systems include reduced labour costs, increases in productivity, and enhanced efficiency in operations.
The application of AMRs is widely used for moving parts within production lines in manufacturing as well as to facilitate picking and packing in a warehouse. E-commerce companies also use AMRs to expedite the order fulfilment process by effective movement of products from the storage areas to shipping zones. This provides the opportunity for companies to easily combine stability with flexibility through an AMR due to its flexibility in integration with any existing conveyor system. Advanced Sensor Systems for Intelligent Conveyor Systems
Another trend pushing the performance of material handling systems concerning efficiency is advanced sensing on conveyor systems. Some of the types include proximity, photoelectric, and laser sensors that make real-time data collection based on the performance of conveyors. Laser sensors measure the speed and linearity of the item stream and give feed forward towards jam prevention and stable streams of goods.
AI and Machine Learning Impact Conveyor System
Artificial intelligence and machine learning change conveyor systems with smart optimization, predictive maintenance, and real-time monitoring. AI algorithms could analyze large amounts of operation data to find bottlenecks, optimize load balancing, and regulate conveyor speed according to workload for maximum efficiency. Machine learning models learn based on past performance data to predict when some equipment might fail, hence allowing the maintenance teams to address issues in advance.
The other feature is that AI-based conveyor systems also provide advanced real-time monitoring and control. For example, temperature, vibration, and speed sensors with AI can be utilized for the assessment of these parameters and for checking system health and operation status at any time. The real-time insight so generated helps the business make informed data-driven decisions and thus enhance quick response to demands or unforeseen problems.
Future Trends and Challenges
Advantages in the development of technologies relate more to recent and upcoming trends, among them 5G connectivity, edge computing, and digital twin models, to which conveyor systems will add further improvements
5G connectivity will come with greater data transmissibility under dependable conditions as well; this means when the situation requires heavy operation, conveyor systems with real-time monitoring and operation from afar, will use the available resources.
Advantages include a data return mechanism at the closest point since when brought, it ensures that any collected data may not prolong its response while such collected data enables super-fast responses of an automatically guided conveyor system. Digital twins - virtual replicas of physical systems, can be used to simulate the conveyor operation and identify possible problems with workflow optimization and proactive maintenance planning. With this trend, however, comes an increase in the level of cybersecurity as digital and connected conveyor systems can be a source of security threats. It is henceforth important to protect them against cyber threats to allow continued operation and safeguard information.
Automation, though cutting manual labour, requires skilled personnel for supervising, managing, and maintaining sophisticated systems and therefore, training and staff development are an important investment in companies embracing the newest conveyor technology.
Conclusion
The future of conveyor systems will centre on automation, AI, and sensor technologies, transforming traditional conveyors into intelligent, adaptive systems that make them efficient in material handling.
Companies seeking to be competitive must explore and adopt these emerging technologies and set a course for efficiency, fewer downtimes, and versatility. With the right approach, modern conveyor systems can revolutionize material handling, helping businesses realize their operational goals and support growth in an increasingly digital world.